In the realm of manufacturing and engineering, precision is the key that unlocks doors to innovation, efficiency, and reliability. One such advancement that has been making waves in various industries globally is the use of Cold-Drawn Welded Tubes, a technological marvel that has redefined the standards of precision in tubing. This article explores the significance of Cold-Drawn Welded Tubes and how they are elevating standards worldwide.
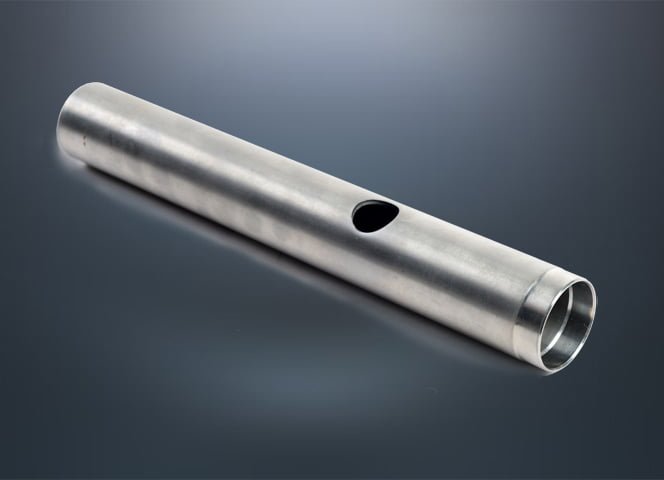
The Art of Cold Drawing: Unveiling the Process
At the heart of this technological leap is the cold drawing process. Unlike traditional methods, where hot-formed tubes undergo multiple processes to achieve the desired dimensions, cold drawing involves pulling the tube through a die at room temperature. This meticulous process ensures dimensional accuracy, a smoother surface finish, and improved mechanical properties.
The precision achieved through cold drawing is unparalleled. The tubes are not only consistent in size but also exhibit enhanced strength and durability. This makes them ideal for applications where reliability is non-negotiable, such as in the automotive, aerospace, and construction industries.
Global Applications: Where Precision Meets Performance
Cold-Drawn Welded Tubes have found applications in a myriad of industries, thanks to their exceptional precision and reliability. In the automotive sector, these tubes are becoming the preferred choice for components that demand tight tolerances and structural integrity. Whether it’s for chassis components or fuel systems, the precision of cold-drawn tubes ensures optimal performance and safety.
In aerospace, where lightweight yet robust materials are crucial, cold-drawn tubes have become an integral part of manufacturing processes. The tubes’ ability to withstand extreme conditions while maintaining precision makes them indispensable in the production of aircraft components.
The construction industry, too, has embraced cold-drawn tubes for their superior quality. From structural elements to architectural designs, the precision of these tubes ensures that every project meets stringent standards.
Environmental Impact: A Sustainable Approach
Beyond their precision and reliability, Cold-Drawn Welded Tubes also offer environmental benefits. The cold drawing process consumes less energy compared to traditional hot-forming methods. This not only reduces production costs but also aligns with the growing global emphasis on sustainable manufacturing practices.
As industries worldwide seek eco-friendly solutions, the adoption of Cold-Drawn Welded Tubes represents a step towards achieving environmental goals without compromising on performance or quality.
Global Outreach: Meeting Diverse Industry Needs
The demand for precision knows no borders, and Cold-Drawn Welded Tubes are answering the call on a global scale. Manufacturers and suppliers are now reaching out to international markets, providing a wide array of industries with access to these high-precision solutions.
Whether it’s a construction project in Asia, an automotive assembly line in Europe, or an aerospace venture in North America, Cold-Drawn Welded Tubes are becoming a staple, proving that precision is a universal language that resonates across industries and geographies.
Conclusion: Shaping the Future with Precision
In the dynamic landscape of modern industry, where efficiency, reliability, and sustainability are paramount, Cold-Drawn Welded Tubes stand as a testament to precision perfected. By elevating standards worldwide, these tubes are not just components; they are the building blocks of a future where technology and precision converge to shape a world of possibilities. As industries continue to evolve, the role of Cold-Drawn Welded Tubes in defining new benchmarks for precision is destined to leave an indelible mark on the global stage.