In the realm of modern manufacturing, precision and efficiency are paramount, especially when it comes to crafting components for critical applications like automotive engineering. The High-Frequency Welding Process stands out as a cornerstone in the production of Precision Electric Resistance Welded (ERW) tubes, playing a pivotal role in shaping these versatile and essential components. This article unravels the intricate process, shedding light on how Precision ERW Tubes take shape through high-frequency welding.
1. Introduction to Precision ERW Tubes:
Precision ERW Tubes are renowned for their uniformity, durability, and seamless integration into various industrial applications. At the heart of their production lies the High-Frequency Welding Process, a method that ensures the tubes meet the rigorous standards demanded by industries such as automotive manufacturing.
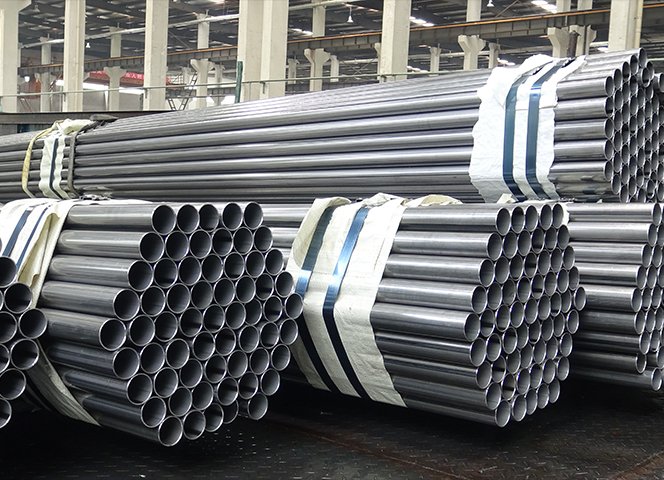
2. Starting with Coils:
The journey of a Precision ERW Tube begins with coiled strips of metal, typically steel. These coils serve as the raw material that will undergo a series of transformations to become the high-quality tubes known for their structural integrity.
3. Curling and Deforming:
The first step in shaping Precision ERW Tubes involves curling and deforming the coiled strips into the desired tube shape. This process sets the stage for the subsequent welding steps and is crucial in achieving the precise dimensions required for the final product.
4. High-Frequency Welding:
The hallmark of Precision ERW Tube production is the High-Frequency Welding Process. High-frequency electric current is employed to heat the edges of the curled and deformed strip to the point of fusion. This seamless welding technique creates a strong and durable bond between the edges, forming a continuous tube.
5. Eliminating Internal and External Burrs:
Post-welding, the tubes undergo a meticulous finishing process to eliminate any internal or external burrs. This step is critical in ensuring the cleanliness and quality of the final product, as burrs can compromise the functionality and structural integrity of the tube.
6. Cleanness and Efficiency:
The High-Frequency Welding Process contributes significantly to the cleanness and efficiency of Precision ERW Tubes. The controlled and precise nature of this welding method minimizes the need for additional cleaning processes, streamlining production and reducing waste.
7. Energy-Saving Attributes:
Compared to traditional welding methods, the High-Frequency Welding Process is energy-efficient. The focused application of electric current results in minimal heat dissipation, making this method not only precise but also environmentally friendly, aligning with the growing emphasis on sustainable manufacturing practices.
8. Lightweight Features:
The welding process plays a crucial role in determining the weight and strength characteristics of the final tube. Precision ERW Tubes, thanks to high-frequency welding, are known for their lightweight features without compromising on structural integrity, contributing to fuel efficiency in applications such as automotive design.
9. Quality Control and Consistency:
The use of high-frequency welding allows for greater control over the quality and consistency of Precision ERW Tubes. Manufacturers can fine-tune the welding parameters to meet specific standards, ensuring that each tube meets the exacting requirements of the intended application.
10. Meeting Industry Demands:
The High-Frequency Welding Process is a response to the demands of industries that require precision, efficiency, and reliability in their components. Precision ERW Tubes, born from this advanced welding technique, have become a staple in various sectors, including automotive, where stringent standards are paramount.
In conclusion, the High-Frequency Welding Process is the driving force behind the creation of Precision ERW Tubes, bringing together efficiency, cleanness, and energy-saving attributes. As industries continue to evolve, this welding method stands as a testament to the commitment to innovation and precision in modern manufacturing.